In large format printing, the development of inks and ink technology has always been a balancing act. Print service providers have traditionally been forced to choose between durability, flexibility, print speed, media compatibility and environmental impact. Each ink type, whether eco-solvent, latex or UV, comes with its own compromises.
With AQUAFUZE, Fujifilm has introduced a new approach to ink chemistry that combines the best of water-based and UV-curable technologies while solving many of their long-standing limitations. This is not simply an improvement – it’s a materials science breakthrough that could reshape how the industry thinks about inkjet production.
In this article, Shota Suzuki, one of the lead developers behind AQUAFUZE ink technology, elaborates on the thinking, chemistry and technical hurdles that led to this innovation.
It all started with chemistry
My background is in synthetic organic chemistry, specialising in the development of new materials for industrial applications. I never started out thinking I’d work in inkjet, but the materials science perspective I was able to bring has been critical in tackling some of the toughest challenges in inkjet R&D.
One of the biggest of these challenges was stabilising UV-curable materials in a water-based system. That’s something the industry has been trying to crack for years. Water and UV monomers don’t naturally mix – they’re chemically incompatible. Bringing them together in a stable, printable and curable form took us nearly a decade of research at Fujifilm’s R&D centres in Japan.
When we started developing AQUAFUZE, we deliberately set out to avoid the compromises we saw in existing ink technologies. Some water-based UV systems on the market rely on water-soluble photo-initiators and monomers, which are prone to degradation and can shorten shelf life. Others, like latex inks, require very high curing temperatures, limiting media choice and increasing energy costs. Traditional UV-curable inks, while durable, don’t offer the same health and safety requirements in terms of odour and safety labelling that today’s customers expect. So, in developing AQUAFUZE, we knew we had to take a fundamentally different materials science approach – develop a stable, water-based UV-curable ink that avoids water-soluble components, cures at low temperatures, and eliminates the need for primers or optimisers. That’s what sets AQUAFUZE apart.
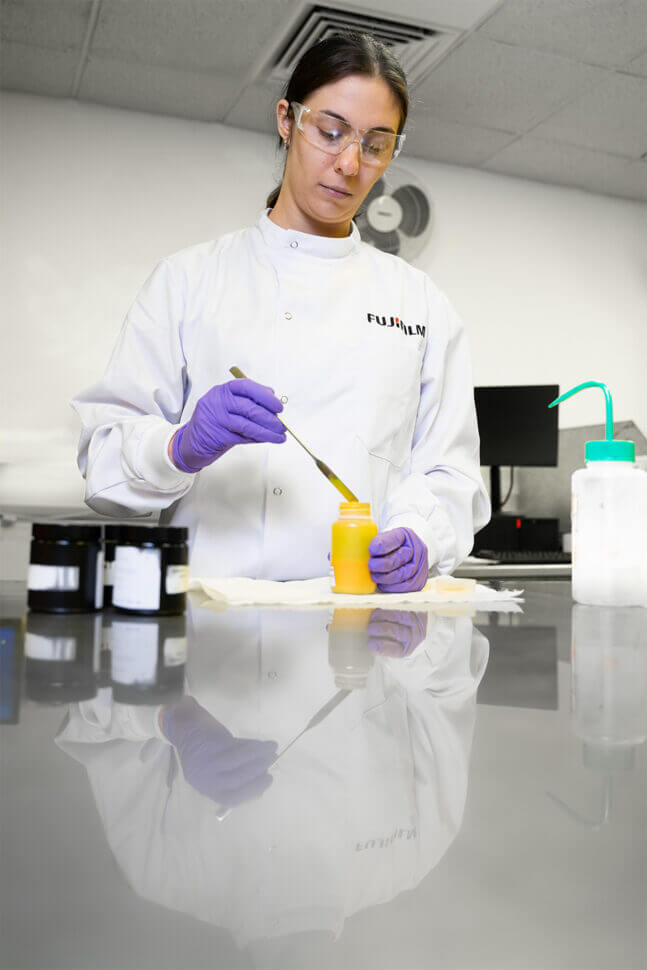
Emulsion is the key
We drew on knowledge from other areas of Fujifilm, including our work on thermo/pressure sensitive recording materials. This cross-disciplinary thinking led us towards emulsion design as the starting point.
At the heart of AQUAFUZE is a proprietary UV-curable emulsion. Traditionally, UV-curable monomers are extremely sensitive to water, leading to degradation or premature cross-linking if not properly handled.
Our breakthrough came when we developed a custom dispersant system. This system allows us to contain UV-reactive materials in such a way that they remain isolated from water until the exact moment of UV curing. This level of control meant we could achieve the storage stability and print performance we needed, all while using low-energy LED UV lamps for curing.
Why we avoided water-soluble photo-initiators
One of the critical decisions we made was to avoid water-soluble photo-initiators and monomers entirely. Other attempts to develop water-based UV ink systems have relied on these, but from a chemistry standpoint, I was concerned about the risks.
Aside from being relatively expensive, water-soluble photo-initiators and monomers tend to react too easily with water, which raises issues around premature decomposition and shelf-life instability.
Instead, in a true industry first, we focused on developing non-water-soluble photo-initiators and monomers. We worked hard to develop a dispersion process that would keep these initiators and monomers stable and uniformly distributed throughout the ink. This decision has paid off in long-term ink stability and highly reliable curing performance – both of which were non-negotiable for the large format print market.
Addressing real-world problems
Beyond the lab, we knew AQUAFUZE had to solve practical production problems for print providers. With solvent inks, long outgassing times can delay finishing. Latex inks require high curing temperatures, which can cause media distortion and drive up energy costs.
With AQUAFUZE, prints are ready for finishing immediately after LED UV curing, rather than having to wait hours, or even a full day. The curing temperature is low, around 40 to 45 degrees Celsius, so even heat-sensitive substrates can be printed without issue.
Another key feature I’m proud of is that AQUAFUZE inks don’t require primers or optimisers. The adhesion properties we built into the ink mean it sticks well to a wide range of media straight out of the printer. This simplifies workflows and reduces overall ink consumption and additional consumable costs. Moreover, the ink doesn’t require an overcoat, as latex ink does, due to the high durability of UV ink..
We’ve also ensured that the ink formulation is low odour and carries no hazardous substance labelling, making it safer for operators.
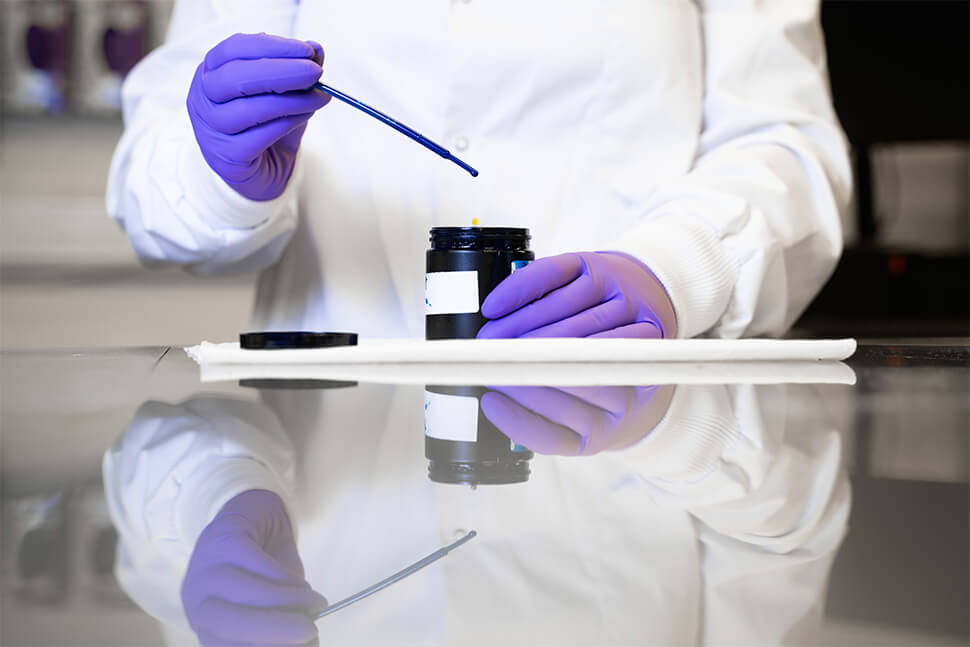
Because the chemistry behind AQUAFUZE is so different from conventional inkjet inks, existing printers weren’t compatible. This meant we had to develop a hardware platform that could handle the unique properties of AQUAFUZE. This resulted in the development of the Acuity Triton – the first printer designed specifically for this ink. Of course, that’s just the starting point. We’re already in discussions about expanding AQUAFUZE compatibility to other platforms.
Looking ahead
Right now, AQUAFUZE ink is available in CMYK colours, and we’re seeing strong interest from industries like signage, wallcoverings, and vehicle graphics. But we’re not stopping there.
We’re actively exploring options for a higher speed/productivity machine, especially for customers with higher-volume production needs.
AQUAFUZE was developed as a direct response to what print providers have been telling us for years: they want inks that deliver durability and versatility without the compromises of existing technologies. Whether it’s reducing drying times, lowering energy consumption, or eliminating the need for hazardous chemicals, our goal was always to solve real customer pain points.
By combining water-based chemistry with UV durability and low-temperature curing, we’ve created more than just another ink. I genuinely believe AQUAFUZE represents a new category of wide format inkjet technology – one that blends the best of both worlds.
As customer expectations continue to evolve, materials science will remain central to inkjet innovation. AQUAFUZE is proof that when you approach ink development from a chemistry-first perspective, you can create solutions that truly change what’s possible in print production.
It’s been an exciting journey, and for us, this is just the beginning.
Shota Suzuki, Technical Manager at FUJIFILM Speciality Ink Systems Ltd